Torque sensors have capacity range from 5 Nm, 10 Nm, 20 Nm, 50 Nm, 100 Nm to 200 Nm. Torque sensor capacity can be customized according to customer requirements.
After purchasing one ATO torque sensor, you can buy a special digital controller to obtain readings directly, or buy a transmitter to output standard signal to PLC, DCS and other systems. Customized output signal is 0~5V, 0~10V, 0~±10V, or 4-20mA.
Specification
Model |
ATO-DYJN-102 |
Shipping Weight |
2kg |
Capacity Range * |
0-5 Nm ~ 0-200 Nm |
Sensitivity |
1.0-2.0mV/V |
With Transmitter |
ATO-LCTR-OA |
Zero Balance |
±2%FS |
Non-linearity |
0.2%FS |
Hysteresis |
0.05%FS |
Repeatability |
0.05%FS |
Creep |
0.05%FS/30min |
Temperature Drift on Zero |
<0.05%F.S/10℃ |
Temperature Effect on Output |
<0.05%F.S/10℃ |
Operating Temperature |
-20℃~+80℃ |
Humidity |
0~90%RH |
Impedance |
350Ω |
Insulation Resistance |
≥5000MΩ/100VDC |
Stability |
0.3%FS/year |
Safety Overload |
120%F.S |
Ultimate Overload |
150%F.S |
Excitation Voltage |
DC 5-15V |
Material |
Alloy steel |
Protection Class |
IP65 |
Electrical Connection |
5 pin circular connector (Packing included) |
Cable Length |
3m (Φ3mm) (Packing included) |
Wiring |
EXC+: Red, EXC-: Black, SIG+: Green, SIG-: White |
Torque Sensor Dimension (unit: mm)

Feature

- 42CrMo alloy steel material with good hardenability and strong mechanical fatigue resistance.
- Industrial high-precision strain gauges have high measurement accuracy, small creep, small thermal hysteresis and good long-term stability.
- Aviation plug is ready to plug and unplug, convenient and quick, can ensure the transmission signal high speed and stability.
Torque Sensor Force Point
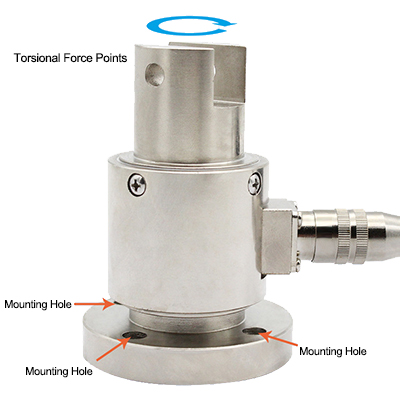
Application
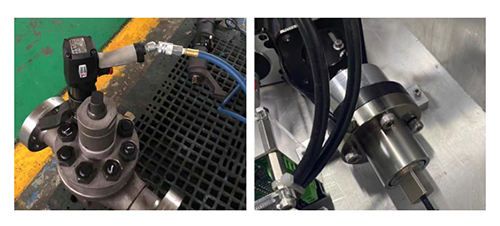
Tips: Torque sensor fails to return to zero after unloading
There are two conditions if the torque sensor fails to return to zero after installation or unloading the load. The first is the torque sensor connection. The second is overload.
If the reaction torque sensor still displays the value of 0.1-1 Nm after loading and unloading, it is usually caused by the inconsistent stopping positions of the power terminal and load terminal in the measurement process. Remove the torque sensor and inspect the sensor signal zero point. If it is normal, it is indeed caused by the inconsistent stopping positions of the power terminal and load terminal.
If the sensor zero point fails to go back to zero when the torque sensor is overloaded, the torque display is inaccurate in the measurement process, and the zero point still doesn't go back to zero after dismantling the sensor, such a condition can be basically confirmed to be caused by the overloaded sensor.
The fundamental reason is that the selected range of the sensor is inaccurate or smaller. In normal conditions, in selecting the sensor range, it should be 1.5 times-2 times of the maximum torque value on site. For instance, if the on-site power terminal is the motor, the motor power is 6Kw and the revolving speed is 1500, then the torque should be 38.19N.m after the conversion, and the torque sensor range should be 1.5 times to 2 times of the maximum torque value, because the moment torque in starting the motor is very high, generally higher than the rated torque of the motor.