How to Choose a Centrifuge Machine
Centrifuge machines are widely used in various laboratories such as hospital laboratories, scientific research institutions laboratories, food and drug testing laboratories, and food hygiene laboratories. Centrifuge selection should pay attention to the following aspects.
Rotational Speed
Centrifuge machines can be divided into low-speed centrifuges (≤6000r/min), high-speed centrifuges (≤25000r/min), and ultra-high-speed centrifuges (≥30000r/min) according to the rotational speed.
- When the particle diameter of the material is between 1 micron and 50 microns, it can be separated by a low-speed centrifuge. The rotation speed is about 4000 rpm to 7000 rpm, and the relative centrifugal force is about 2000g to 9420g. Generally, a desktop low-speed centrifuge or a floor-standing low-speed large-capacity centrifuge is used.
- When separating viruses and other substances in animal and plant tissues with a diameter of about 0.1 micron to 1 micron, it is recommended to use a high-speed refrigerated centrifuge with a rotation speed of 10,000 rpm to 20,000 rpm and a centrifugal force of about 10,000g to 100,000g.
- When separating various proteins, DNA, RNA and other components with a diameter of about 0.002 microns to 0.1 microns, an ultracentrifuge is required, the speed of which is above 40,000 rpm, and the centrifugal force shall reach 100,000g up to 400,000g.
Separation Performance
Separation performance is the most basic function, including separation effect, washing effect, processing capacity, degree of automation, etc. Due to differences in material properties, including material viscosity, density, and slurry solid-liquid ratio, it is difficult to accurately determine the final separation effect. When the solid phase material is a crystalline product, and the degree of crystal damage during separation is required to be low, the selection of the centrifuge must be based on the size and concentration of solid particles in the suspension (or emulsion), solid and liquid (or two liquids) density difference, liquid viscosity, filter residue (or sediment) characteristics.
Generally speaking, the separation factor is an important factor affecting the separation effect of the centrifuge. The separation factor is related to the rotating speed of the drum and the diameter of the drum, and is proportional to the square of the angular velocity of the drum.
Washing refers to the washing of the filter cake. For some materials, the filter cake needs to be washed with washing liquid, and some even need to be washed several times to meet the requirements, which requires a washing tube. The effect of washing and the time of washing have a lot to do with the aperture, arrangement position and structure of the washing tube. The processing capacity of the centrifuge is related to the physical and chemical properties of the material and the separation requirements, and is generally estimated by the number of cycles per hour and the quality of the filter cake in a single operation.
Temperature Control Performance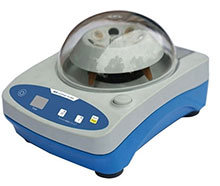
When separating some organic active substances such as enzymes, refrigerated centrifuges are selected when it is necessary to maintain a constant temperature during the separation process. There are low-speed refrigerated centrifuges and high-speed refrigerated centrifuges. Then according to the required speed, the rotor capacity can choose the appropriate centrifuge machine.
Corrosion Resistance
The materials separated by the centrifuge are generally corrosive to a certain extent, and the materials of the parts in contact with the materials must be able to meet the requirements of corrosion resistance to ensure safe use. Structural parts material, gasket material, surface treatment measures, and filter cloth material should be determined during model selection. The properties of the materials (chemical properties, temperature during separation, etc.) can be informed to our company during model selection, so that our company can make suggestions on the selection of centrifuge materials according to the characteristics of the separated media, and indicate them in the order to ensure centrifuge machine meets the anti-corrosion requirements.
Explosion-proof Performance
If the materials processed by the centrifuge contain flammable and explosive substances such as organic solvents, the centrifuge should have explosion-proof performance. When the material contains flammable and explosive items such as Benzene, toluene, petroleum ether, cyclopentane; dichloroethane, carbon tetrachloride, methanol, ethanol, ether, methyl ethyl ether, acetone, cyclohexanone, ethylene glycol-ethyl ether, ethylene glycol-butyl ether, Formaldehyde, acetaldehyde, pyridine, an explosion-proof centrifuge should be selected. The explosion-proof performance depends on the explosion-proof requirement level of the process.
In the explosion-proof occasions of the past, only the preparation of explosion-proof motors is proposed. In the last two years, for the occasions where the processed materials contain organic solvents, most of them have put forward the requirements for protection against bad gas. In fact, to achieve explosion-proof in the true sense, various measures can be taken in the preparation of mechanical and electrical accessories, such as the use of explosion-proof motors, explosion-proof lighting, anti-static belts, anti-collision measures, safety interlocks, hydrogen protection devices, non- Contact dynamic braking, electrostatic grounding, automatic explosion-proof control, etc. Therefore, the customer must specify the characteristics of the medium to be separated and the explosion-proof requirements and grades when ordering.