3 phase 30 hp vertical centrifugal pump for sale. It is a single-stage centrifugal pump with 61m3/h maximum flow, 63m minimum head, 73m maximum head and 80mm diameter of inlet and outlet.
Features:
- The centrifugal pump has a vertical structure, and its inlet and outlet have the same diameter. The inlet and outlet are on the same centerline so that they can be installed in the pipeline like a valve. If a protective cover is added, it can be used in the open air.
- Easy to install and maintain. There is no need to dismantle the piping system, just remove the connecting flat nut of the vertical pump. All rotor parts can then be removed.
- The vertical pump can be installed vertically or horizontally according to the requirements of the piping system.
- Vertical centrifugal pumps can be run in series or in parallel according to the requirements of flow and head.
Specification
- Model: ATO-VCP-100-200
- Power: 30 hp (22kW)
- Number of stages: Single stage
- Input voltage: AC 220V~480V
- Input frequency: 50Hz/60Hz
- Inlet diameter: 100mm (4 inch)
- Outlet diameter: 100mm (4 inch)
- Flow (min. flow to max. flow): 70m3/h (308 gpm), 100m3/h (440 gpm), 130m3/h (572 gpm)
- Head (max. head to min. head): 54m (177ft), 50m (230ft), 42m (207ft)
- Efficiency: 65%, 74%, 42%
- Installation mode: Vertical type or horizontal type
- Nominal diameter of impeller: 200mm
- Size: 480*475*850mm
- Weight: 217kg
Vertical centrifugal pump dimension (unit: mm):

Boundary dimension |
L |
B |
H |
C1*B1 |
480 |
475 |
850 |
160*200 |
Installation dimension |
A |
C2*B2 |
4-Φd1 |
140 |
110*170 |
4-Φ18 |
Flange dimension |
D |
D1 |
n-φd |
φ200 |
φ160 |
8-φ18 |
Details
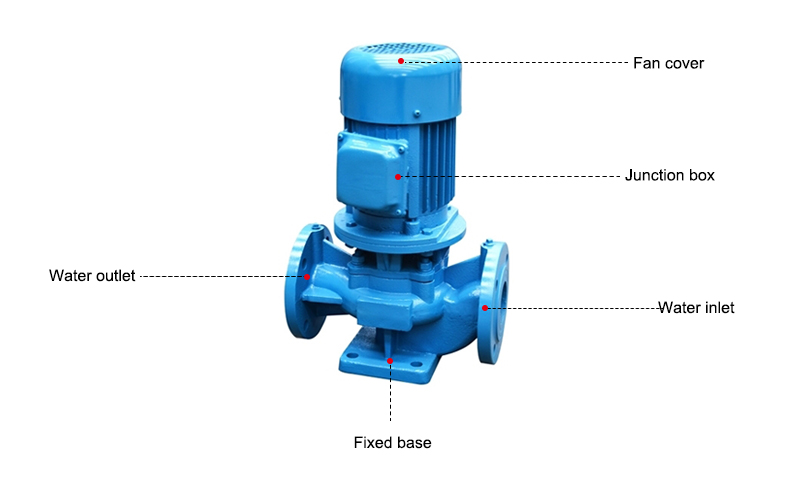
Tips: 4 methods to control the flow of the centrifugal pump
At present, the centrifugal pump is the most widely used pump product and it is widely used in the oil and gas, petrochemical, steel, power, food and beverage, chemical, pharmaceutical and water treatment industries. How to economically and effectively control the output flow of centrifugal pumps has triggered wide discussion. It was once popular to use variable frequency speed control to control the output flow, and to cancel the control flow of all control valves. From the current point of view, there are four methods that are frequently used in the market: outlet valve opening adjustment, bypass valve adjustment, adjustment of impeller diameter, and speed control.
- Outlet valve opening adjustment: In this method, the pump is connected in series with the outlet pipeline regulating valve. The actual effect is like using a new pump system. The large output head of the pump is not changed, but the flow curve is attenuated.
- Bypass valve adjustment: In this method, the valve is connected in parallel with the pump, and its actual effect is like using a new pump system. The large output head of the pump changes, the flow curve characteristics also change, and the flow curve approaches the line shape.
- Adjustment of impeller diameter: This method uses no external component. The flow characteristic curve changes as the diameter changes.
- Speed control: The impeller speed change directly changes the flow curve of the pump, and the characteristics of the curve do not change. When the revolving speed decreases, the curve becomes flat, and both the pressure head and mass flow are reduced.
The overall efficiency of the pump system, both the outlet valve adjustment and the bypass adjustment method increase the pipeline pressure loss and the pump system efficiency is greatly reduced. The impeller diameter adjustment has little effect on the efficiency of the entire pump system, and the speed control method basically does not affect the system efficiency, as long as the speed is not lower than 50% of the normal speed.
Dynamic consumption level
Assume that the output flow of the centrifugal pump is adjusted from 60m3/h to 50m3/h by the above four methods, and the power consumption when the output is 60m3/h is 100% (the pressure head at this time is 70m), how do these flow control means affect the consumption power of the pump?
- The power consumption is 94% for the outlet valve opening adjustment, and the consumed power is rather high when the flow is relatively low.
- Bypass adjustment. The pressure head of the bypass valve is reduced to 55M. This can only be realized y increasing the flow of the pump. As a result, the power consumption increases by 10%.
- Adjust impeller diameter. After reducing the impeller diameter, the output flow and pressure of the pump reduce accordingly, and the power consumption decreases to 67%.
- Control speed. When the revolving speed reduces, both the pump flow and pressure head reduce, and the power consumption decreases to 65%.