Air conditioning refrigerant pressure sensor is specially designed for HVAC system, supporting the measurement of liquid or gas media, its pressure range covers 0 ~ 0.6/0.8/1/1/1.4/1.6/1.8/2.5/3/4MPa optional, the working temperature range of -40 ~ 85 ℃, adapt to the extreme cooling and heating environments, protection grade IP65. With IP65 protection, compact design and light weight, it is easy to install and has 10g vibration resistance and 500g/ms shock resistance, high durability, ideal for refrigeration system.
Specification
Model |
ATO-CYYZ41 |
Measuring Medium |
Liquid/gas (compatible with contact material) |
Pressure Range |
0~0.6/0.8/1/1.4/1.6/1.8/2.5/3/4MPa |
Temperature Range |
-40~85℃ |
Output Signal |
4-20mA/0-5V/1-5V |
Pressure Type |
Positive and negative pressure, sealed pressure (absolute pressure 101.3kPa as zero point) |
Turn-on Time |
20ms |
Power Supply |
9~32VDC |
Maximum Power |
≤0.02W |
≤0.08W |
4-20mA |
0-5V/1-5V |
Response Frequency |
100Hz |
Accuracy Class |
0.5%FS (including repeatability≤0.1%FS, hysteresis≤0.1%FS) |
Reference conditions: Temperature 15~25°C; Humidity 45~75%RH |
Stability |
±0.1% FS/year |
Temperature Compensation |
-10 to 70°C |
Temperature Drift |
±0.02% FS/°C (>-10℃) |
±0.05%FS/℃ (<-10℃) |
Protection Class |
IP65 (Note: the protection level is reached when the electrical connection is complete) |
Ambient Temperature |
-40~85°C |
Diaphragm |
316L stainless steel (contact with measured medium) |
Process Connection |
316L stainless steel (contact with measured medium) |
Housing |
316L stainless steel |
Display Housings |
ABS engineering plastic |
Hirschmann Connector |
ABS engineering plastic |
Vibration Resistance |
10g (20-2000Hz) |
Shock Resistance |
500g/ms |
Short Circuit Protection |
Permanent |
Reverse Polarity Protection |
No damage, but not working |
Insulation Resistance |
≥100MΩ, 500VDC |
Insulation Strength |
1*10^6 cycles (lower range to upper range) |
Insulation Strength |
500VAC |
Net Weight |
≈113g |
Details
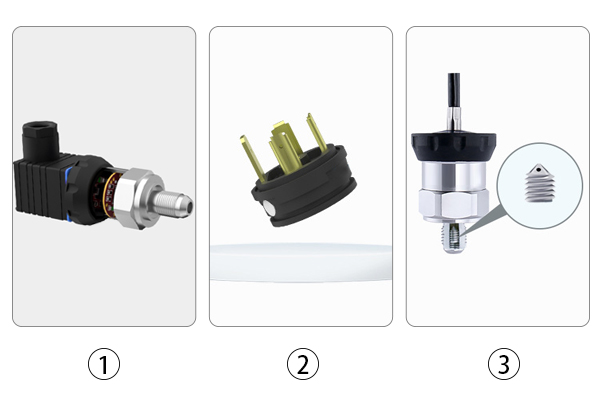
- EMC Electromagnetic: Protection circuit amplification circuit, electromagnetic compatibility refers to the ability of a pressure sensor or system to operate in compliance with the requirements of its electromagnetic environment and does not produce intolerable electromagnetic nuisance to any equipment in its environment.
- Small Details Big Changes: Snap anti-rotation to prevent misinstallation leading to unscrewing the cable.
- Adding a Pulse Snubber: Cavitation, liquid hammer and peak pressures can occur in liquid filling systems, for example when closing valves quickly, or when pumps are started and shut down. This can occur mainly at the inlet and outlet ends, even at very low operating pressures. The sensor is equipped with an internal pulse snubber, which is a good solution to such problems.
Pressure Sensor Dimension Drawing (unit: mm)
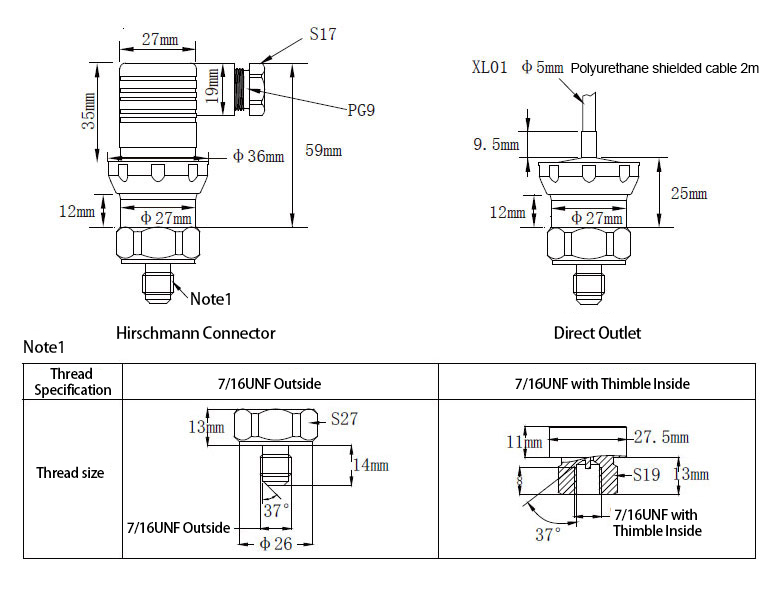
Wiring Diagram

Note:
Circles represent shielded wires, and all marked grounding points must be effectively grounded. It is recommended to use shielded twisted signal cable. In order to avoid ground loops, the shielding layer using a single-ended ground, in the pressure transmitter end of the insulation floating ground, and in the control cabinet end of the ground.
The pressure transmitter shell is grounded by default, so the field equipment needs to be effectively grounded, if the field equipment can not be grounded, it is necessary to make the indicated grounding point effectively grounded.
Applications
Tips: How to install the refrigeration pressure sensor correctly?
The following points need to be noted when installing the freezing pressure sensor:
- Ensure that the interface of the refrigerant pressure transducer matches the system interface exactly and avoid using incompatible threaded connections.
- Before installation, clean the connection parts thoroughly to prevent impurities from affecting the sealing.
- Install the pressure sensor in a location with low vibration and suitable temperature to extend the service life of the equipment.
- When tightening the air conditioning refrigerant pressure sensor sensor, avoid over-tightening to prevent damage to the seal or the internal structure of the sensor.
- After completing the installation, gradually apply a pressure test to check the connection for leakage.