Plunger dosing metering pumps offer precise fluid flow control, making them valuable in scenarios demanding accuracy, such as dosing chemical reagents, formulating pharmaceuticals, treating drinking water, and various industrial processes. They can also handle a wide range of chemicals and are capable of withstanding the most corrosive substances.
Specification
Model |
ATO-DZ-X15/7.6(5.4) |
Flow |
15L/h |
Motor Voltage |
380V 50Hz |
Motor Power (Optional) |
370W |
550W |
Pressure |
5.4Mpa |
7.6Mpa |
Plunger Diameter |
16mm |
Stroke |
20mm |
Pump Speed |
96/144 min-1 |
Pump Head Material |
PVC |
Inlet & Outlet Diameter |
6mm Pipe Sleeve |
Weight |
40kg |
Dimension (Unit: mm)
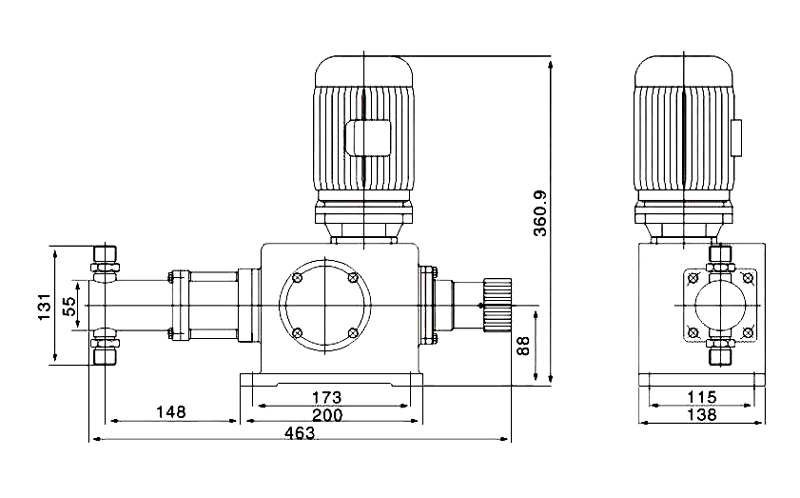
Plunger Dosing Pump Working Principle
Through the reciprocating motion of the plunger, the working medium is directly sucked in or discharged. Since both the plunger and seal are in direct contact with the medium, choosing a jointly made plunger material and seal form can ensure that the pump has more ideal performance during operation.

Tips: What is the purpose of a metering pump?
A metering pump serves the critical function of delivering precise and consistent amounts of liquid, typically in industrial and chemical processes. Its primary purpose is to accurately control the flow rate of a fluid, ensuring that specific volumes or quantities are dispensed with great accuracy. Dosing pumps are widely used in applications such as water treatment, chemical manufacturing, pharmaceutical production, and food processing.
These dosing pumps are designed to handle various fluids, from corrosive chemicals to lubricants, and are crucial for maintaining process efficiency, quality, and safety. By maintaining a constant flow rate, metering pumps can help control chemical reactions, ensure consistent mixing ratios, and prevent wastage, contamination, or environmental harm. They are known for their reliability, precision, and ability to operate under high pressure, making them indispensable tools in industries where accurate and consistent fluid dosing is vital for successful operations.