Nema 23 bipolar stepper motor is a four-wire connection motor with encoder, wire colors of black, green, red and blue, holding torque at 1N·m, step angle accuracy ±5%, low noise and high precision. It is widely used in CNC machine, drawing equipment and sewing machine, robot arm and so on. ATO permanent magnet stepper motor can be controlled by a voltage of DC 24V ~ 50V or AC 20V ~ 40V digital stepper driver for precise position control.
Physical Specification
- Model Number: ATO-FY56EM300A
- Matched the Driver Model: ATO-FYDM504T
- Flanged Size: 57 x 57mm (Nema 23)
- Motor Length: 54mm
- Shaft Diameter: 8mm/ 6.35mm
- Number of Leads: 4 wire
- Weight: 0.7kg
Electrical Specification
- Motor Type: Bipolar Stepper
- Step Angle: 1.8°
- Rated Current: 3A
- Holding Torque: 1 N·m (100 N·cm, 142 Oz.in)
- Phase Resistance: 0.9Ω
- Phase Inductance: 5.2mH
- Rotor Inertia: 260g·cm2
Dimensions (Unit: mm)
L=54mm
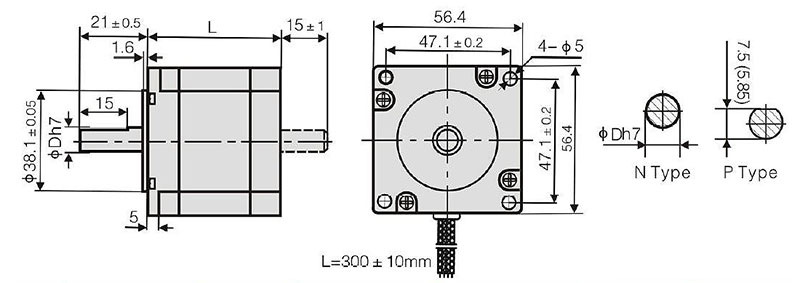
Wiring Diagram

Speed-Torque Curve Diagram

Details

Tips: Stepper motor for CNC machine
CNC machine is generally composed of control media, CNC devices, servo systems, and the machine itself. The first step in the application of stepper motors on CNC machine is to input the compiled program to the CNC system through the control medium. It is actually to convert the compiled program into digital information that can be recognized by the machine.
Then the stepping motor converts the converted digital information into pulse signals through the numerical control device and transmits it to the servo system. The servo system converts the pulse signal from the numerical control device into the precise movement of the moving parts of the machine.
The accuracy of CNC machine is affected by the mechanical parts and transmission components of the machine itself, and the working condition of the servo system directly affects the accuracy of the CNC machine. The so-called servo system refers to an automatic control system that takes position and speed as the control object, also known as a drag system or a follow-up system. The servo system accepts the feed pulse command generated by the interpolation device or interpolation software, and after a certain signal conversion, voltage and power amplification, it is converted into the motion of the machine table relative to the cutting tool.