Nema 23 high torque bipolar stepper motor used in CNC machine, drawing equipment and sewing machine, robot arm and so on. It is a four-wire connection motor with encoder, holding torque at 0.4N·m, step angle accuracy ±5%, no lost step and high precision. ATO permanent magnet stepper motor can be controlled by a voltage of DC 24V ~ 50V or AC 20V ~ 40V digital stepper controller for precise position control.
Physical Specification
- Model Number: ATO-FY56ES250A
- Matched the Driver Model: ATO-FYDM504T
- Flanged Size: 57 x 57mm (Nema 23)
- Motor Length: 41mm
- Shaft Diameter: 8mm/ 6.35mm
- Number of Leads: 4 wire
- Weight: 0.47kg
Electrical Specification
- Motor Type: Bipolar Stepper
- Step Angle: 1.8°
- Rated Current: 4.2A
- Holding Torque: 40 N·cm (0.4 N·m, 57 Oz.in)
- Phase Resistance: 1.4Ω
- Phase Inductance: 1.4mH
- Rotor Inertia: 150g·cm2
Dimensions (Unit: mm)
L=41mm
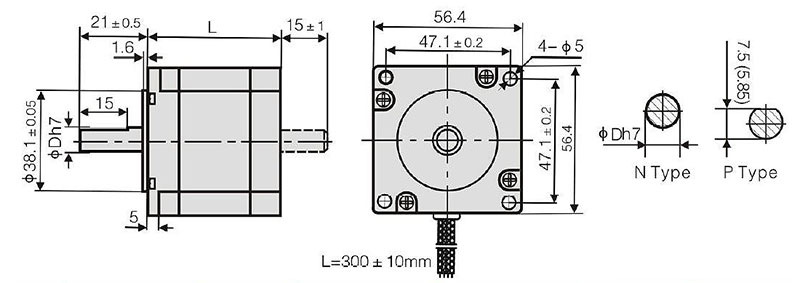
Wiring Diagram

Speed-Torque Curve Diagram

Details

Tips: Factors that determine the step angle of a stepper motor
When the stepper motor switches the excitation current of the stator winding once, the rotor rotates by a fixed angle, that is, the step angle. The step angle is generally obtained from the rotating torque generated by the switched phase current, so the number of poles per phase is required to be an even number. Motors are usually more than two-phase, of course, there are some special single-phase motors with only one coil.
Although it is single-phase, the direction of the magnetic flux generated by a coil reverses alternately to drive the rotor to rotate. The phases of practical motors are single-phase, two-phase, three-phase, four-phase, and five-phase. Most of the stepping motors currently use permanent magnet rotors. The reason why permanent magnets are commonly used is their high efficiency and high resolution.
The factor that determines the step angle is the resolution of the motor. The higher the resolution of the stepping motor (the number of steps per revolution, 360° divided by the step angle), the higher the position accuracy. In order to obtain high resolution, the number of poles should be large. For PM type rotors, N and S poles are alternately placed on the outer surface of the rotor core at equal pitches. The number of rotor poles is the sum of the number of N poles and S poles. To simplify the explanation, assume that the number of pole pairs is 1. Here it is determined that the step angle θs of the motor whose rotor is a permanent magnet is represented by the following formula, where Nr is the number of rotor pole pairs and P is the number of stator phases.