12V 0.4A, 2 phase 6 wires Nema 17 stepper motor, with 1.8 deg. step angle (200 steps/revolution), is perfect for small robotics and automation projects. Cheap price and direct sale by manufacturer.
Specifications
Electrical Specification |
Model |
ATO47-0406A |
Matched the Driver Model |
ATODSP42 (Click it to see more info) |
Step Angle |
1.8° |
Holding Torque |
3.17kg-cm(44oz-in) |
Voltage |
12V |
Rated Current/phase |
0.4A |
Phase Resistance |
30Ω |
Inductance |
38mH |
Rotor Inertia |
68g-cm2 |
Physical Specification |
Frame Size |
42 x 42mm |
Length |
47mm |
Shaft Diameter |
Φ5mm |
Shaft Length |
22mm |
Motor Leads |
6 |
Weight |
0.35kg |
Technical Parameters |
Step Angle Accuracy |
±5% (full step, no load) |
Resistance Accuracy |
±10% |
Inductance Accuracy |
±20% |
Temperature Rise |
80℃ Max. (rated current, 2 phase on) |
Ambient Temperature |
-10℃~+50℃ |
Insulation Resistance |
100MΩ Min. 500VDC |
Dielectric Strength |
1Min. 500VAC·5mA |
Shaft Radial Play |
0.06Max. 450g |
Shaft Axial Play |
0.08Max. 450g |
Quality Assurance |
Warranty Period |
12 months |
Certificate |
CE, ROHs, ISO/SGS9001 |
Nema 17 Stepper Motor Dimension (Unit=mm)
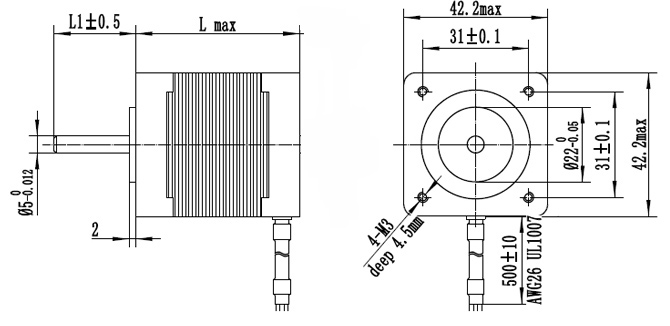
L1=24mm, Lmax=47mm
Nema 17 Stepper Motor Wiring Diagram
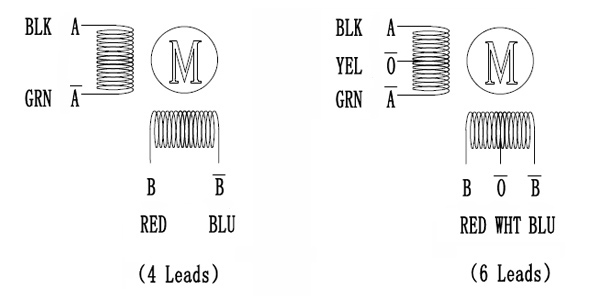
Tips: Why stepper motor cannot start at higher velocity and accompanying whistler?
The stepper motor can run normally at low velocity, and cannot start at certain higher velocity and accompanying whistler.
There is a technical parameter for the stepper motor: no-load start frequency. That is, the stepper motor can normally start pulse frequency under no-load. If the pulse frequency is higher than the value, the motor cannot normally start, the stalling or self-locking may occur. Under the circumstance of load, the start frequency shall be lower. The pulse frequency should have acceleration so that the motor rotates at high velocity. That is, the start frequency is low and then rises to the anticipated high frequency according to the acceleration (the motor runs at from low velocity to the higher one).
Except foregoing reasons, the reason for causing whistler may also be for big load. If the motor rotates at high velocity, the output torque of the motor will decreases. However, if the load requirement cannot be satisfied, stalling of motor will occur and whistler will be changed along with the change in frequency, to which the solution is to reduce the rotational velocity or replace for the motor with larger torque. Besides, after the motor rotates at high velocity and then stops, the transient whistler will be caused, which is resulted from chopping of phase current. It is only necessary to set the automatic semi-flow on the stepper driver board as effective.