An incremental magnetic linear encoder is a precision measurement device used to track the linear position of a moving object. Incremental magnetic scale encoders are commonly used in applications like CNC machines, robotics, and automated assembly lines, where precise positioning is crucial.
Features
- Incremental magnetic linear encoder offers high system accuracy and high repeatability.
- Magnetic linear scale encoder provides high resolution up to 0.1 µm and features high clearance tolerance.
- It is designed for more than 100 million bends of flexible conductors.
- It ensures non-contact measurement, dust resistance, wear resistance, impact resistance, vibration resistance, and magnetic field interference resistance.
Specification
- Model: ATO-LMD
- Supply Voltage: 5V +/-5%
- Magnetic Spacing: 2+2mm
- Resolution: 1μm
- Repetition Accuracy: +1μm
- Output Frequency: 2000 KHz
- Speed: 5m/s
- Cable: 8-Core Shielded Wire
- Wiring Method: Direct Lead Output
- Output Form: RS422
- LED Status Indication: Red/Green
- Electric Current: Less Than 50 mA
- Protection Level: IP67
- Operating Temperature: -20°C~70°C
- Storage Temperature: -20°C~80°C
- Customizable Parameters: Resolution, Output Frequency, Counting Direction, Cable Length (≤ 15m)
Note: If you want to purchase a magnetic scale, please contact us.
Signal Output Diagram
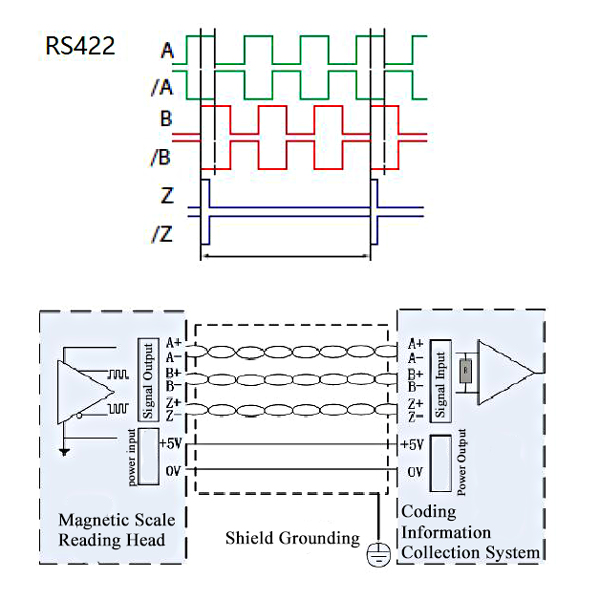
Dimension (Unit: mm)
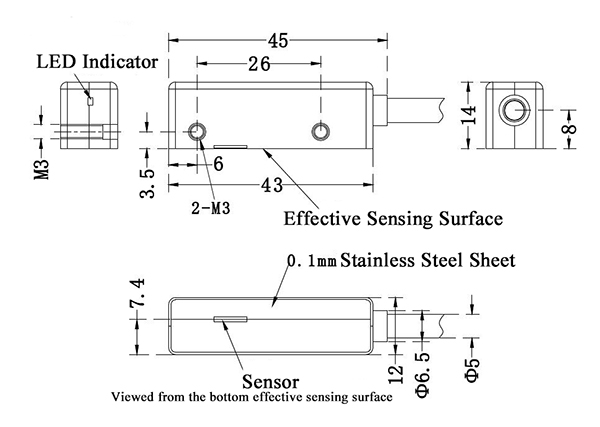
Tips: How does an incremental magnetic linear encoder work?
An incremental magnetic linear encoder works by using a magnetic sensor to detect changes in a magnetic field as it moves along a magnetized scale. The scale, typically a strip of material with alternating magnetic poles (north and south), creates a periodic magnetic pattern. As the encoder's sensor moves along this scale, it generates an electrical signal in response to the changing magnetic field.
The sensor typically contains Hall effect or magnetoresistive elements that convert the magnetic changes into digital signals. These signals are processed to determine the relative position, speed, and direction of movement. Unlike absolute encoders, incremental encoders only track changes in position, meaning they need a reference point to determine absolute position. They are commonly used in applications requiring precise control and measurement of linear motion, such as CNC machines, robotics, and industrial automation systems.