Hydraulic orbital motor is widely applied in agriculture machinery, fishing machinery, plastic industry, mining, and construction machinery, especially fitted to lower load applications, such as plastic injection mold machines, cleaners, grass cutters, winches, conveyors, slews, sweeper drives, augers, cutters, mowers and chippers.
Specification
Model |
ATO-OMP-305 |
Shaft Type (Optional) |
Flat Key, Splined |
Flange Type (Optional) |
2 Bolts, 4 Bolts |
Displacement |
305 cc/rev (305 cm3/rev) |
Working Pressure |
15 MPa |
Flow |
Continuous |
57 LPM |
Intermittent |
68 LPM |
Max.Speed |
Continuous |
203 rpm |
Intermittent |
242 rpm |
Pressure |
Continuous |
100 ∆Bar |
Intermittent |
124 ∆Bar |
Torque |
Continuous |
412 Nm |
Intermittent |
483 Nm |
Weight |
8.5kg |
Note:
- A simultaneous maximum torque and maximum speed are not recommended.
- ∆Bar refers to true pressure difference between inlet port and outlet port.
- Continuous Rating means that the motor may be run continuously at these ratings.
- Intermittent operation refers to that the motor running time must not exceed 10% per minute under this condition.
*To assure the best orbital motor life, run it for approximately one hour at 30% of rated pressure before application to full load. Be sure this motor is filled with fluid before any load applications.
Dimensions (Unit: mm)
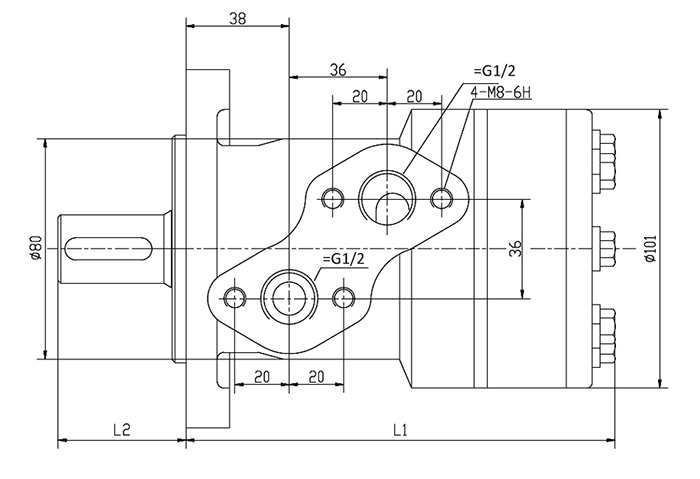
L1=187mm
Hydraulic Orbital Motor Shaft (Unit: mm)
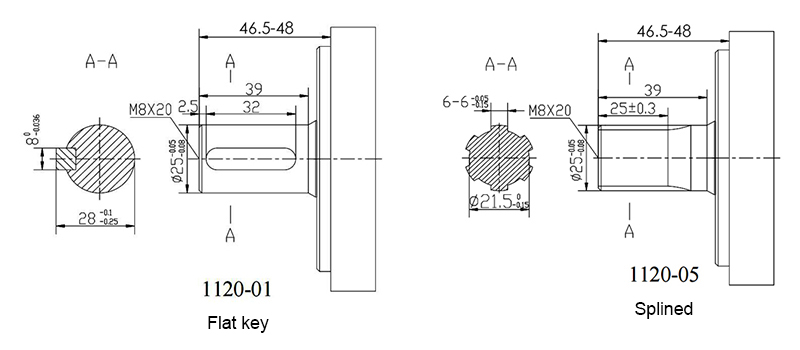
Flange Types (Unit: mm)
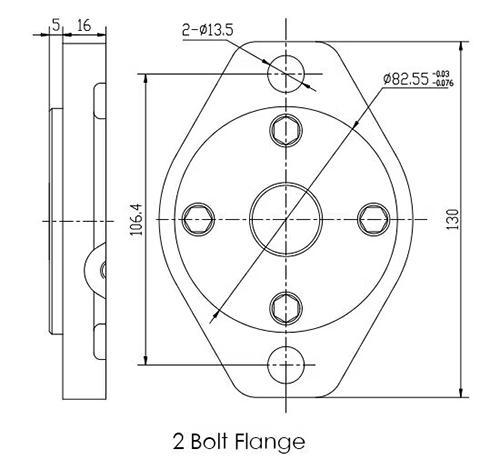
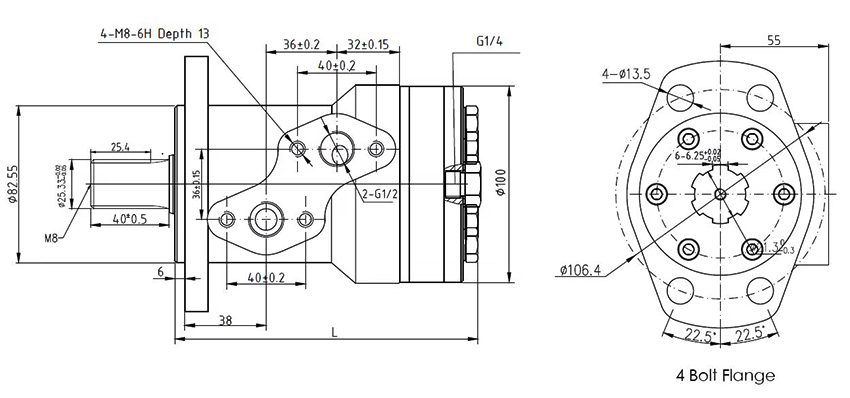
L=194mm
Details

Tips: Structure of the hydraulic orbital motor
- Internal meshing gear pair composed of rotor and stator. The cycloid pin wheel meshing pair is the torque-generating part. The stator is fixed on the shell together with the partition plate and the back cover to form seven tooth cavities which only communicate with the oil distribution holes of the shell one by one.
- Oil distribution mechanism is composed of an oil distribution sleeve and shell. The two ring grooves of the oil distribution sleeve are respectively communicated with the oil inlet and return ports of the shell. Its twelve longitudinal grooves are connected with six oil inlets, and the six oil return channels form the oil distribution link with the oil distribution holes of the shell.
- The splines at both ends of the linkage shaft are respectively connected with the rotor and the output shaft. Its function is to transmit the torque and ensure the synchronization of the oil distribution sleeve and the output shaft with the rotor.
- The function of the output shaft is to output the torque generated by the rotor through the linkage shaft and drive the oil distribution sleeve to rotate synchronously.