Portable 3D gyroscope sensor with four-point M4 screw mounting design, small size, easy to install, strong adaptability. Operating voltage (9~36V), low power consumption (40mA), both high performance and low energy consumption, widely used in robotics, precision machinery and vehicle control and other fields, to provide reliable and accurate angle and angular velocity measurement solutions.
Specification
Model |
ATO-ML7300-1-A |
Measuring Axial |
Z axis |
Angle of Azimuth Measuring Range |
±180° |
Angular Velocity |
Measurement range <450°/S |
Acquisition Band Width |
>1000Hz |
Resolution |
0.1°/S |
Operating Life |
5 years |
Non-linear |
0.1% of FS |
Temperature Compensation |
Full temperature range, -45℃~85℃ |
Temperature Drift |
<±0.2°/sec |
Power-on Startup Time |
3s |
Auto Output Rate |
5Hz output, 15Hz, 35Hz, 50Hz can be set (RS485 without this function) |
Output Signal |
RS232/RS485/RS422/TTL/CAN |
Average Trouble-Free Operating Time |
≥45000 hours/time |
Negative Tenderness |
20000g, 2ms, 1/2sine |
Vibration Resistant |
10grms, 10~1000HZ |
Waterproof Rating |
IP67 |
Cable |
Standard 1.5 meters length, wear-resistant, oil-resistant, wide temperature, shielded cable 5*0.2mm2 |
Connector |
6-pin aviation plug |
Tolerance Load |
1000 |
Operating Voltage |
9~36V |
Operating Current |
40mA |
Operating Temperature |
-40℃~85℃ |
Storage Temperature |
-55℃~125℃ |
Connector |
Lead wire (1.5m) or waterproof aviation socket |
Housing Material |
Aluminum alloy frosted oxidation |
Mounting |
Four M4 screws |
Dimensions |
60*59*29mm |
Net Weight |
180g |
Dimensional Drawing (unit: mm)
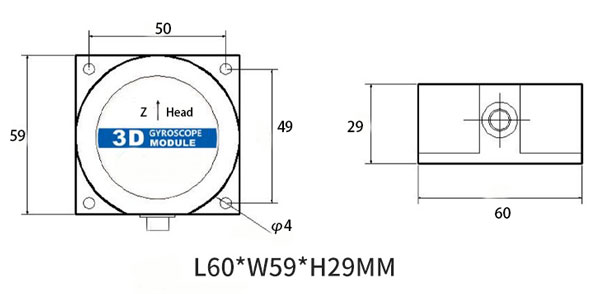
Axis Direction
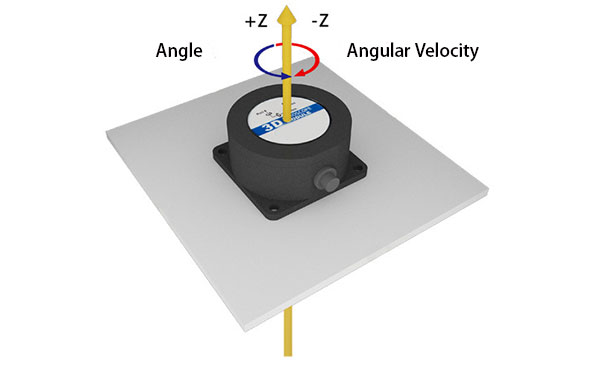
ATO-ML7300 is mainly used for the navigation of robotic vehicles, AVG vehicles, and the attitude control of UAVs. This gyro sensor is not affected by magnetic field interference, so it can measure the yaw angle normally in the magnetic field area, only need to set the desired zero-deviation angle (±180°/0-360°), which can replace the function of electronic compass without being affected by the magnetic field.
Wiring Drawing
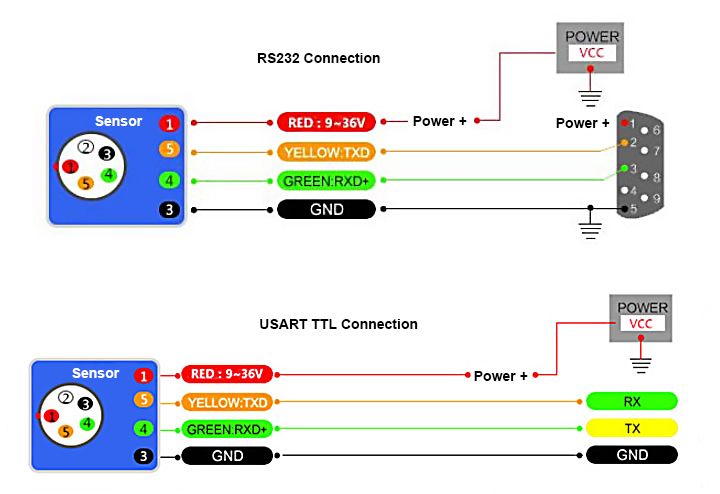
Applications
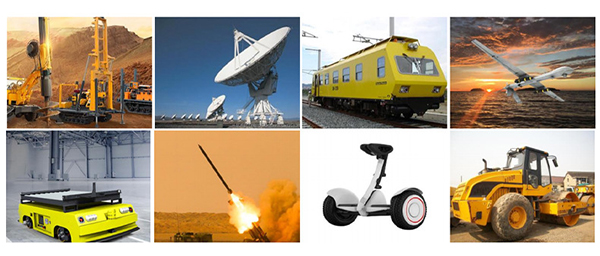
Tips: How to calibrate and improve the accuracy of a single-axis gyro sensor?
To ensure the accuracy of the sensor data, the calibration steps are very important:
- Static Calibration: Place the sensor in a no-motion state and record zero offset data.
- Dynamic Calibration: Verify the output value at a known rotation rate and adjust the deviation.
In addition, care should be taken to minimize the effects of ambient noise and temperature drift, for example by adding a shield around the sensor or using temperature compensation algorithms. Choosing a high-quality signal processing chip can also significantly improve measurement accuracy.