Small single-axis or triaxial capacitive accelerometer sensor for sale. It is widely used in vibration, shock, rotation acceleration and inclination measurement, calibration, industrial monitoring and other measurements. ±1/5/50g measurement range, up to 2000Hz frequency response, nonlinear error less than 0.5%.
Specifications
Model |
ATO-SADR01 |
ATO-SADR05 |
ATO-SADR50 |
ATO-SADR301 |
ATO-SADR305 |
Sensitivity |
1000 mV/g (±10%) |
250 mV/g (±10%) |
38 mV/g (±10%) |
1000 mV/g (±10%) |
38 mV/g (±10%) |
Axis |
Single Axis |
Three Axis |
Measuring Range |
±1g |
±5g |
±50g |
±1g |
±50g |
Vibration Nonlinearity |
0.5% |
Maximum Lateral Sensitivity |
<5% |
Frequency Response |
0~1000Hz (±10%) |
0~2000Hz (±10%) |
0~400Hz (±10%) |
0~1000Hz (±10%) |
0~400Hz (±10%) |
Resonant Frequency |
5500Hz |
15000Hz |
20000Hz |
5500Hz |
20000Hz |
Noise |
~1 mV (rms) |
~1.5 mV (rms) |
~1.5 mV (rms) |
~1 mV (rms) |
~1.5 mV (rms) |
Zero G Bias Voltage |
2.5±0.1V DC |
Operating Voltage |
+5~+16V DC |
Operating Temperature |
-40~+120℃ |
-40~+85℃ |
-40~+100℃ |
-40~+120℃ |
-40~+100℃ |
Shock Resistance (No Power Supply) |
2000g |
2000g |
3000g |
2000g |
3000g |
Sensitivity Temperature Coefficient |
0.3%/℃ |
0.5%/℃ |
0.8%/℃ |
0.3%/℃ |
0.8%/℃ |
Weight |
20g |
16g |
Case Material |
Stainless steel |
Aluminum alloy |
Output Method |
Three-core overall shielded cable (2m) |
Five-core overall shielded cable (2m) |
Installation Method |
4-Φ2.8 or adhesive |
Features
- This SADR series axial capacitive accelerometer sensor has single-axis or tri-axis output.
- Can measure static acceleration, such as gravity acceleration and inclination and other physical measurements, high sensitivity, stable performance.
- Low voltage and current, low power consumption, strong anti-interference ability.
- Acceleration sensor total weight <20g, small size and light weight, more convenient installation.
Dimension (unit: mm)

Working Principle

Capacitive accelerometer sensors use micromachining technology to machine a variable gap differential capacitive sensitive element on a silicon wafer. As shown in the figure below, the differential capacitance is composed of two fixed pole plates and one movable pole plate, where the movable pole plate is connected to the inertial mass block, i.e. the cantilever beam shown in the figure. The motion of the cantilever beam causes a change in the differential capacitance, which is then amplified, converted and detected by a circuit integrated on the same silicon wafer to output a voltage signal proportional to the acceleration.
The SADR series of single-axis/triaxial capacitive accelerometer sensors require at least a single +5V or +3V DC power supply to interface with standard data acquisition systems. The sensitivity and 0g DC bias voltage values are proportional to the supply voltage. The output voltage increases from the 0g output value for positive acceleration and decreases for negative acceleration.
When subjected to acceleration, the DC output voltage value is: Vout=Vs/2+ (sensitivity x a x Vs/5)
where Vs is the supply voltage in V and a is the acceleration value in g.
The AC output voltage value is: Vout= Sensitivity x a
Wiring Diagram
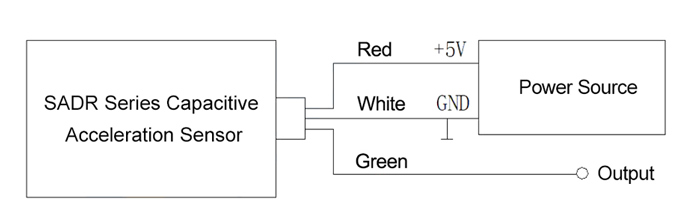
Tips: What is capacitive accelerometer sensor?
The capacitive accelerometer is a type of sensor used to measure acceleration by detecting changes in capacitance. It operates on the principle that when an object experiences acceleration, there is a relative movement between the sensor's internal components, typically a fixed electrode and a movable electrode (mass). This movement alters the distance between these electrodes, thereby changing the capacitance.
The sensor consists of a proof mass suspended between a set of fixed electrodes. When the accelerometer experiences acceleration, the proof mass shifts slightly from its equilibrium position. This shift causes a change in the capacitance between the proof mass and the fixed electrodes. The sensor's electronics then convert this capacitance change into a voltage signal, which is proportional to the acceleration.
Capacitive accelerometers are favored for their high sensitivity, low noise, and ability to measure both static (e.g., gravity) and dynamic (e.g., vibration) accelerations. They are commonly used in applications such as vibration monitoring, structural health monitoring, consumer electronics (like smartphones), automotive systems (e.g., airbags), and inertial navigation systems.
Their advantages include low power consumption, high resolution, and good stability over a wide temperature range, making them suitable for both industrial and consumer applications.