Three phase 380V AC to 12V/ 18V/ 24V DC plating rectifier power supply is 5000A adjustable output current, air cooling mode, with complete protection functions, energy saving more than 20% because of higher conversion efficiency, especially low DC output voltage.
Application: This kind of plating rectifier is mainly used in the brush plating process, suitable for repairing plated workpieces with defects, depositing different metal patterns on metal surfaces and electrolysis degreasing and plating process etc.
Parameter
Model |
ATO-HI-5000 |
Input Voltage |
Three phase AC 380V/ 400V/ 415V/ 440V/ 460V/ 480V (optional, 220-1000V voltages are customizable) |
Input Frequency |
50Hz/60Hz |
Output Current |
0-5000A (continuously adjustable by 1A) |
Output Voltage |
DC 0-12V/ 0-18V/ 0-24V/ 0-36V/ 0-48V (optional, 8-500V voltages are customizable) Note: Output voltage is adjustable by 0.1V. |
Output Frequency |
15kHz |
Output Current Stability |
≤1% |
Output Voltage Stability |
≤1% |
Efficiency |
≥92% |
Power Factor |
≥0.9 |
Operation Mode |
Remote control or manual control |
Module |
IGBT module |
Cooling Method |
Air cooling |
Start-up Postponing Time |
≤10s |
Limiting Current Value |
Io±5A (Io is the rated current) |
Limiting Voltage Value |
Vo±5A (Vo is the rated current) |
Signal Interface |
RS485, PLC 0-10V, 4-20mA |
Modulation Mode |
PWM control |
Complete Protection Functions |
Over current, over voltage, over heat, short circuit, phase lack, input undercurrent protection, over temperature, and diode defect. |
Protection Grade |
IP20 |
Ambient Temperature |
-10℃-50℃ |
Relative Humidity |
≤80% |
Size |
680*550*1250mm |
Net Weight |
260kg |
Certification |
CE, ISO |
Warranty |
12 months |
Plating Rectifier Main Technical Features
- Operation mode: Remote control or manual control is optional.
- Output control mode: One-way pulse and two-way pulse output control for optional.
- Constant output control mode: Constant current and constant voltage control modes can be selected.
- Soft start time: Soft start working time can be set in the range of 0-200s.
- High control accuracy: Control accuracy ≤ ± 1%.
- Rectification mode: IGBT inverter soft switch rectification, PWM pulse step modulation, IGBT chopper control mode.
- Pulse pacing frequency range: 1000-8000Hz.
- Man-machine operation interface: PLC color touch screen.
- Main controller: DSP microcomputer digital trigger control, PWM pulse width adjustment control, pulse phase shift resolution ≤1μs.
- Main protection functions: AC power phase loss, overvoltage, undervoltage, fast fuse blowing alarm and circuit breaker protection; output overcurrent, current limit protection, output short circuit, instantaneous overload protection; IGBT switch module, fast rectifier components, switching rectifier transformer, busbar copper bus overtemperature and overheating, fan overheating or water pressure is too high/low, blocking PWM trigger pulse protection.
- Communication method: CAN bus, PROFIBUS, ETHERNET industrial Ethernet, RS485, and RS232 optical fiber communication can be configured according to customer needs to achieve remote group control or monitoring.
- With 1-5 stage constant current slow rise and slow down stage number control, each stage oxidation current and oxidation time can be set separately.
- Real-time recording of multiple process parameters and real-time curves such as forward and reverse current / voltage, pulse current/voltage amplitude, pulse duty cycle, pulse frequency, oxidation time, bath temperature, etc.
- Remote operation control box: The remote operation control box can be configured according to the customer's site conditions, the plating rectifier and the remote control box are separated to prevent, the field operation is more convenient, and the rectifier's corrosion protection is significantly enhanced.
- 5 sets of process parameters can be stored or recalled to shorten the processing programming time.
- Can be connected to the computer through the RS485 communication interface, or stored in the U disk and transferred to the computer, which is convenient for the customer to save the file and analyze the product process quality of the oxidized workpiece.
- Workpiece coating quality: Compactness, smoothness and corrosion resistance are significantly better than ordinary plating process.
Rectifier Controller Features
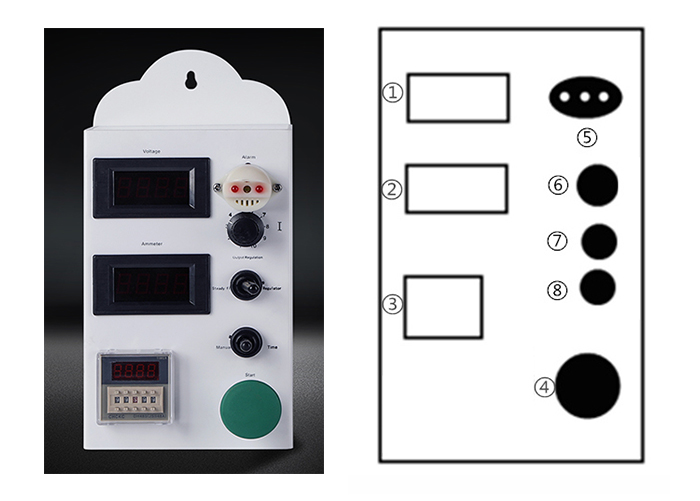
① |
Voltmeter |
② |
Ammeter |
③ |
Timer |
④ |
Start-up |
⑤ |
Alarm Lamp |
⑥ |
Output Regulation |
⑦ |
Steady Current / Steady Voltage |
⑧ |
Manual / Timing |
Details

Tips: The principle of pulse plating rectifier power supply
Understand the principle of pulse plating rectifier power supply can use plating rectifier more correctly. Pulse plating rectifier is a powerful method to improve the coating quality through the control method outside the tank. Compared with ordinary DC plating, it has more excellent properties (such as corrosion resistance, wear resistance, high purity, electrical conductivity, welding and good resistance to discoloration, etc.), and can greatly save rare and precious metals, therefore, it is better used in functional electroplating. At present, the square wave pulse is mostly used in pulse plating.
The pulse plating rectifier power supply can generate a square wave pulse current. When it is used in electroplating, it cannot obtain an ideal square wave, but a waveform similar to a trapezoid, which will affect the full play of the beneficial effect of the instantaneous high potential of pulse plating. The pulse frequency will also have a greater impact on the crystallization of the coating. The frequency is too low and the effect is not obvious. If the frequency is too high, the waveform distortion is large, and even the pulse current will become a DC current. The correct use of the pulse plating rectifier power supply (such as equipment installation, equipment selection, parameter selection, etc.) has an important impact on the pulse waveform, equipment reliability, and normal performance of the advantages of pulse plating.