4000 amps 3-phase AC 480 volt to DC 24 volt electroplating rectifier machine adopts pulse width modulation (PWM) as the control circuit and the main circuit adopts the world famous IGBT power modules, provides higher conversion efficiency. Forced air cooling solution to system thermal problems by using axial fans.
Application: This kind of plating rectifier is mainly used in brush plating process, suitable for repairing plated work pieces with defects, depositing different metal patterns on metal surfaces and electrolysis degreasing and plating process etc.
Specification
Model |
ATO-HI-4000 |
Input Voltage (Optional)* |
Three phase AC 380V/ 400V/ 415V/ 440V/ 460V/ 480V (220-1000V voltages are customizable) |
Input Frequency |
50Hz/60Hz |
Output Current |
0-4000A (continuously adjustable by 1A) |
Output Voltage (Optional)* |
DC 0-12V/ 0-18V/ 0-24V/ 0-36V/ 0-48V (8-500V voltages are customizable) Note: Output voltage is adjustable by 0.1V. |
Output Frequency |
15kHz |
Output Current Stability |
≤1% |
Output Voltage Stability |
≤1% |
Efficiency |
≥92% |
Power Factor |
≥0.9 |
Operation Mode |
Remote control or manual control |
Module |
IGBT module |
Cooling Method |
Air cooling |
Start-up Postponing Time |
≤10s |
Limiting Current Value |
Io±5A (Io is the rated current) |
Limiting Voltage Value |
Vo±5A (Vo is the rated current) |
Signal Interface (Optional)* |
RS485, PLC 0-10V, 4-20mA |
RS485 Interface Function |
Can be used to monitor parameters, control voltage & current values, and remotely start/stop the rectifier. |
Control Box (Included) |
Can adjust the output voltage, current and time, with standard 0-30m remote connection cable. Longer cables can be customized! |
PLC Touch Screen (Optional)* |
Plating rectifier connects with PLC touch screen by RS485 interface to display/adjust the voltage, current and time. |
Modulation Mode |
PWM control |
Complete Protection Functions |
Over current, over voltage, over heat, short circuit, phase lack, input undercurrent protection, over temperature, diode defect... |
Protection Grade |
IP20 |
Ambient Temperature |
-10℃-50℃ |
Relative Humidity |
≤80% |
Size |
650*550*1050mm |
Net Weight |
220kg |
Certification |
CE, ISO |
Warranty |
12 months |
Packing Included |
1 x Three Phase Plating Rectifier 1 x Remote Control Box 1 x 0-30m Cable |
Plating Rectifier Main Technical Features
- Operation mode: Remote control or manual control for optional.
- Output control mode: One-way pulse and two-way pulse output control for optional.
- Constant output control mode: Constant current and constant voltage control modes can be selected.
- Soft start time: Soft start working time can be set in the range of 0-200s.
- High control accuracy: Control accuracy ≤ ± 1%.
- Rectification mode: IGBT inverter soft switch rectification, PWM pulse step modulation, IGBT chopper control mode.
- Pulse pacing frequency range: 1000-8000Hz.
- Man-machine operation interface: PLC color touch screen.
- Main controller: DSP microcomputer digital trigger control, PWM pulse width adjustment control, pulse phase shift resolution ≤1μs.
- Main protection functions: AC power phase loss, overvoltage, undervoltage, fast fuse blowing alarm and circuit breaker protection; output overcurrent, current limit protection, output short circuit, instantaneous overload protection; IGBT switch module, fast rectifier components, switching rectifier transformer, busbar copper bus overtemperature and overheating, fan overheating or water pressure is too high/low, blocking PWM trigger pulse protection.
- Communication method: CAN bus, PROFIBUS, ETHERNET industrial Ethernet, RS485, and RS232 optical fiber communication can be configured according to customer needs to achieve remote group control or monitoring.
- With 1-5 stages of constant current slow rise and slow down stage number control, each stage oxidation current and oxidation time can be set separately.
- Real-time recording of multiple process parameters and real-time curves such as forward and reverse current / voltage, pulse current/voltage amplitude, pulse duty cycle, pulse frequency, oxidation time, bath temperature, etc.
- Remote operation control box: The remote operation control box can be configured according to the customer's site conditions, the plating rectifier machine and the remote control box are separated to prevent, the field operation is more convenient, and the rectifier's corrosion protection is significantly enhanced.
- 5 sets of process parameters can be stored or recalled to shorten the processing programming time.
- Can be connected to the computer through the RS485 communication interface, or stored in the U disk and transferred to the computer, which is convenient for the customer to save the file and analyze the product process quality of the oxidized workpiece.
- Workpiece coating quality: Compactness, smoothness and corrosion resistance are significantly better than the ordinary plating process.
Rectifier Controller Features
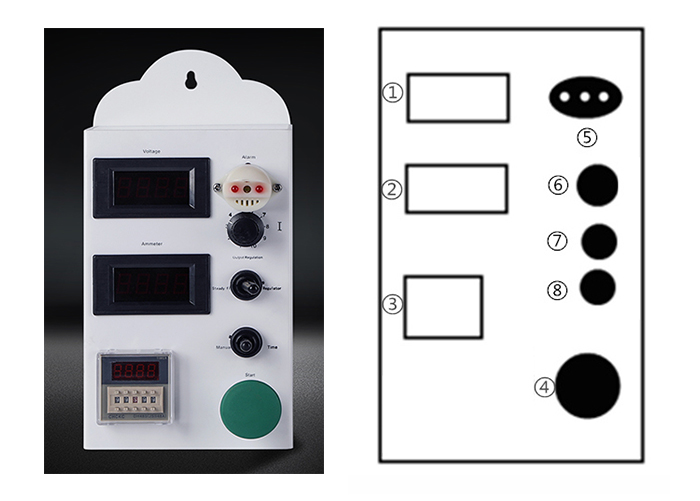
① |
Volmeter |
② |
Ammeter |
③ |
Timer |
④ |
Start-up |
⑤ |
Alarm Lamp |
⑥ |
Output Regulation |
⑦ |
Steady Current / Steady Voltage |
⑧ |
Manual / Timing |
Details

Tips: High frequency plating rectifier in power system
In the power system, the DC power supply is used as a power source for relay protection, automatic devices, control operation circuits, lights, sound signals, and accident lighting. It is a relatively important equipment in power plants and substations. Accidents caused by DC power supply failures occur from time to time, so the reliability and stability of the DC power supply have high requirements. In recent years, many DC power supply manufacturers have introduced intelligent high-frequency plating rectifier switching power supplies. This power supply system has many advantages: Safety, reliability, high degree of automation, smaller size and weight, high overall efficiency, and low noise. To meet the needs of power grid development, it is worth promoting. Therefore, the DC power supply used in the power system is gradually changing from the traditional phase-controlled power supply to the modular high-frequency electroplating rectifier switching power supply.
The working principle of the high-frequency plating rectifier switching power supply is: AC power is connected to the rectifier module, converted into DC after filtering and three-phase full-wave rectifier, and then connected to a high-frequency inverter circuit to convert DC to high-frequency AC. Finally, after passing through the high-frequency transformer, rectifier bridge and filter, the output is smooth DC. This high-frequency switching power supply is mainly composed of a high-frequency switching charging module, a centralized monitor and a battery pack, etc., wherein the charging module and the centralized monitor have a built-in microprocessor, and the degree of intelligence is high. When the high-frequency switching power supply system is running normally, the output of the charger runs in parallel with the battery pack to supply power to the regular load.