2hp stainless steel electric motor with 2 pole, 50/ 60Hz frequency and IE 4 efficiency. This kind of three phase synchronous motor is widely used in fields with high hygiene requirements such as food, chemical industry, medical equipment, etc.
Features
- Smooth stainless steel enclosures easy to clean and sanitize.
- IP65 for water protection rating ensures suitability for clean in place washdown procedures.
- Encapsulated windings prevent any water and moisture from reaching the windings.
- Low surface temperature with less operation costs due to high efficiency.
Specification
Model |
ATO-IEC-802 |
Rated power |
2hp (1.5kW) |
Rated voltage |
208V~230V/ 460V |
Number of pole |
2P |
Phase |
3 phase |
Cooling method |
TEFC |
Frequency |
50/ 60Hz |
Raged speed |
2950r/min |
Mounting type |
B3/ B5/ B14 |
Stainless steel |
304 |
Protection grade |
IP65 |
Insulation class |
Class F |
Protect Feature |
Waterproof |
Efficiency |
IE 4 |
Weight |
39kg |
Certificate |
CE, UL |
Warranty |
12 months |
Dimension

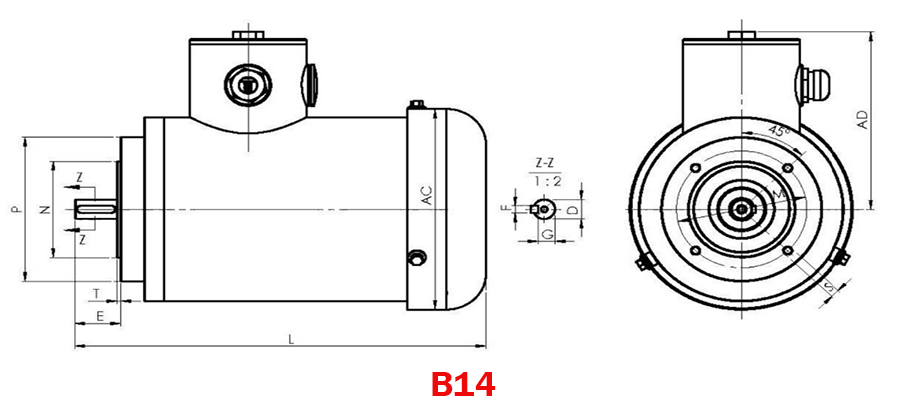

Mounting type |
Frame size |
Mounting dimensions (mm) |
A |
A/2 |
B |
C |
D |
E |
F |
G |
H |
K |
M |
N |
P |
R |
S |
T |
Flange Hole |
Shaft Hole |
AB |
AC |
AD |
B3 |
80 |
125 |
62.5 |
100 |
50 |
19 |
40 |
6 |
15.5 |
80 |
10 |
- |
- |
144 |
- |
- |
- |
- |
M6 |
150 |
156 |
135 |
B14 |
- |
- |
- |
- |
19 |
40 |
6 |
15.5 |
- |
- |
100 |
80 |
120 |
0 |
M6 |
3 |
4 |
M6 |
- |
144 |
135 |
B5 |
- |
- |
- |
- |
19 |
40 |
6 |
15.5 |
- |
- |
165 |
130 |
200 |
0 |
12 |
3.5 |
4 |
M6 |
- |
144 |
135 |
Details
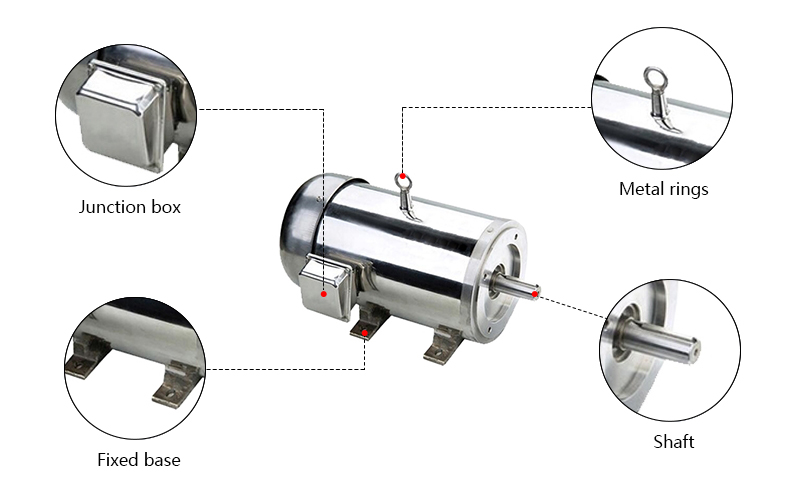
Tips: The Working Principle of a Stainless Steel Motor.
The working principle of a stainless steel motor is based on the interaction of the stator rotating magnetic field (the composite magnetic field generated by the three-phase current in the stator winding) and the rotor current (the current in the rotor winding).
When the symmetrical three-phase winding of the stator is connected to the three-phase power supply, a symmetrical three-phase current will flow into the winding, and a rotating magnetic field will be generated in the space. The magnetic field rotates along the inner circumference of the stator. When the magnetic field rotates, the conductor of the rotor winding is cut. The magnetic flux will generate an induced electromotive force E. Due to the existence of the electromotive force E, a rotor current I will be generated in the rotor winding. According to Ampere’s law of electromagnetic force, the interaction between the rotor current and the rotating magnetic field will produce an electromagnetic force F (the direction of which is determined by the left-hand rule). The direction of rotation is the same, and the rotor is subjected to this torque to rotate according to the direction of rotation of the rotating magnetic field. However, the rotation speed n of the rotor is always smaller than the rotation speed n0 of the rotating magnetic field (called synchronous speed), because if the two speeds are equal, the rotor and the rotating magnetic field do not move relative to each other, and the rotor conductor does not cut the magnetic flux, and the induced electromotive force cannot be generated. With current, there is no electromagnetic torque, and the rotor will not continue to rotate. Therefore, the speed difference between the rotor and the rotating magnetic field is the main factor to ensure the rotation of the rotor.