The 2D electronic compass module (single board) uses advanced magnetic sensing technology to provide accurate heading measurement. The single board has a compact structure and is easy to integrate into embedded systems and devices.
Features
- It is a high-precision two-dimensional electronic compass module that measures azimuth 0~360° with high reliability.
- 2D electronic compass module uses an industrial-grade single-chip microcomputer with strong anti-interference ability and a high-precision magnetic sensor and driver chip, integrating hard magnetic and soft magnetic interference compensation technology. The electronic compass function can be easily and quickly integrated into various products.
- The compass module is small in size and low in power consumption. It can be used in many fields such as antenna stability, vehicles, system integration, etc. High seismic resistance and high reliability also enable the compass to work normally in extremely harsh environments.
Specification
Model |
ATO-SCM220 |
Range |
0-360° |
Accuracy |
1° |
Working voltage |
DC +5V |
Working temperature |
-40~+70℃ |
Working current |
40mA |
Volume |
33*27*8mm (customizable) |
Output |
RS232/RS485/TTL/RS422/Modbus (optional) |
Performance Indicators |
Compass heading parameters |
Heading accuracy |
1° |
Resolution |
0.1° |
Repeatability |
0.3° |
Heading angle |
Navigation tilt angle range |
+/-5° |
Heading angle measurement range |
0~360° |
Calibration |
Hard iron calibration |
✔ |
Soft iron calibration |
✔ |
Magnetic field interference calibration |
one rotation of the plane (two-dimensional calibration) |
Physical characteristics |
Dimensions |
L33xW27xH8 (mm) |
Weight |
5g |
RS-232/RS485 interface connector |
5-pin |
Interface characteristics |
Startup delay |
<50ms |
Maximum sampling rate |
50 times/second |
RS-232 communication rate |
2400~19200 baud rate |
RS-485 communication |
Optional |
TTL communication |
Optional |
Output format |
Hexadecimal |
Power supply |
Supported voltage |
DC+5V |
Current (maximum) |
40mA |
Operating mode |
30mA |
Environment |
Storage range |
-40℃~+125℃ |
Operating temperature |
-40℃~+70℃ |
Vibration resistance |
2500g |
Note: The default horizontal installation (when the compass is placed horizontally, the roll and pitch angle outputs are zero degrees), and the connector needs to be installed vertically downward (when the compass is placed vertically downward, the roll and pitch angle outputs are zero degrees). Please specify when ordering.
Dimension (mm)
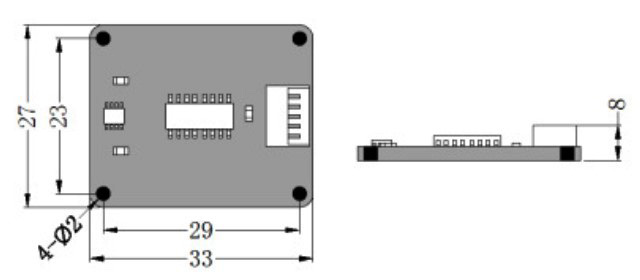
Electrical Connection
Line Color Function |
RED |
WHITE |
BLACK |
GREEN |
YELLOW |
1 |
2 |
3 |
4 |
5 |
VCC |
NC |
GND |
RXD |
TXD |
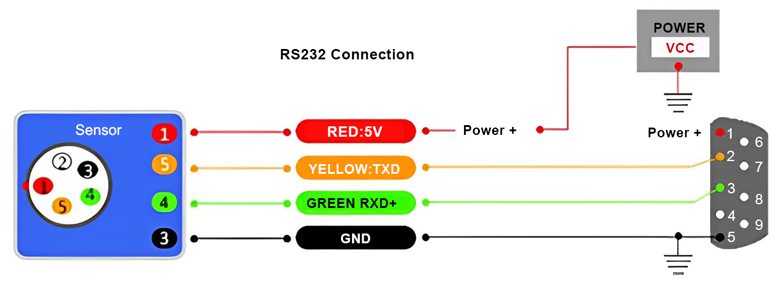
- RS485 and Modbus Wiring Definition
Line Color Function |
RED |
WHITE |
BLACK |
GREEN |
YELLOW |
1 |
2 |
3 |
4 |
5 |
VCC |
NC |
GND |
(B, D+) |
(A, D+) |
Line Color Function |
RED |
WHITE |
BLACK |
GREEN |
YELLOW |
1 |
2 |
3 |
4 |
5 |
VCC |
NC |
GND |
RXD |
TXD |
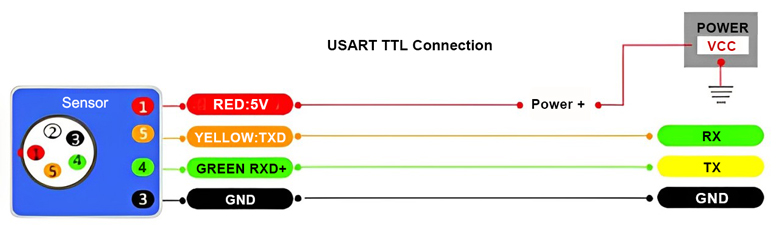
Line Color Function |
RED |
BLACK |
GREEN |
YELLOW |
WHITE |
BROWN |
1 |
2 |
3 |
4 |
5 |
6 |
VCC |
GND |
RXD- (B-) |
RXD+ (A+) |
TXD+ (A+) |
TXD- (B-) |
Applications
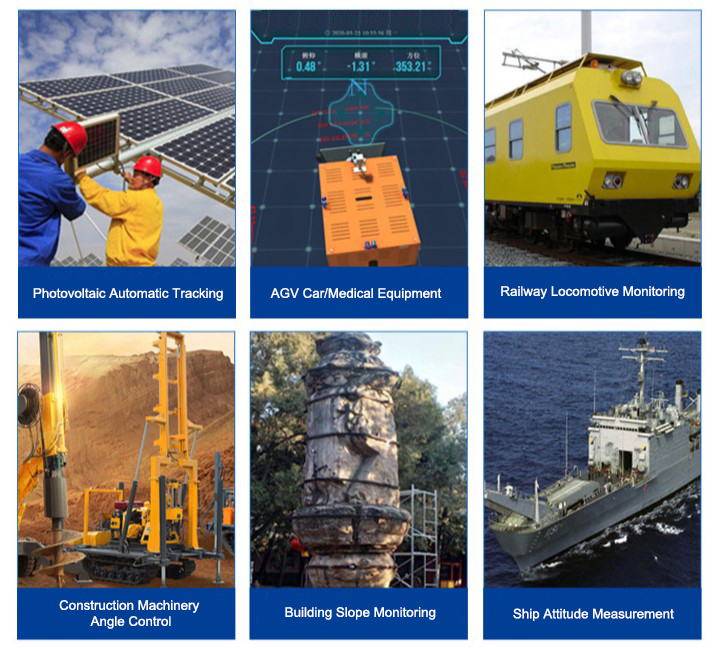
Installation
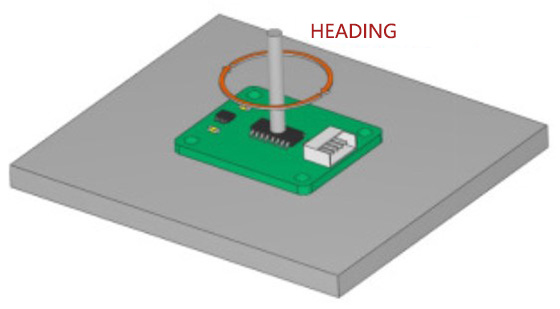
Tips: Precautions for installing 2D electronic compass module
Although the SCM220 electronic compass module can compensate for magnetic interference, users should choose an environment with minimal magnetic interference for installation and use. It is recommended to install 2D electronic compass module away from iron, nickel, magnets, engines, and other magnetic materials. If these magnetic sources are present nearby, maintain a minimum distance of 0.5 meters. To ensure optimal measurement accuracy, use non-magnetic screwdrivers and non-ferrous screws during installation. Strong magnetic materials (such as magnets and electric motors) should be kept at least 10 cm away from the compass, as closer proximity may cause irreversible degradation of measurement accuracy.
Each electronic compass module comes with a 10 cm cable, with an optional length depending on user needs. While 2D electronic compass module can compensate for magnetic deviation in a stable magnetic environment, it cannot compensate for changing magnetic interference. For example, wires carrying DC current generate a magnetic field, and if the current changes, the magnetic field strength will vary accordingly. Batteries are another potential source of changing interference. Since each installation environment will have a different magnetic field, users must evaluate the feasibility of installation in their specific environment.
The compass module has a heading accuracy of 1°, which has been rigorously verified. Proper scientific testing methods are equally crucial. Our recommended testing method is to mount it on a vertical aluminum (or other non-magnetic material) rod for heading accuracy measurement. Ensure the rod is perpendicular to the rotating platform, and minimize the influence of large external magnetic fields during the test.