110 mm strain wave harmonic drive gearbox with a high torque capacity and rigidity is available. Strain wave gearbox with 30/50/80/100/120 gear ratios provides harmonic gear reduction and increases rotation speed. Small harmonic reducer is the simplest solution for your high-precision motion control applications.
Features
- It is a strain wave harmonic drive gearbox that can automatically adjust the center of the wave generator, which is convenient to use.
- Compact harmonic reducer is available with a high torque capacity and 30~120 high gear ratio.
- 110 mm strain wave gearbox is designed for robots.
Specifications
- Model: ATO-SHF-25-I
- Type: Self-aligning
- Diameter: 110 mm
- Thickness: 37.3 mm
- Gear type: Cylindrical gear reducer
- Installation form: Horizontal
- Input speed: 3500 rpm
- Rated power: 0.1 kW
- Output speed: 0~500 rpm
- Available torque: 1~100 N.m
- Gear ratio: 30, 50, 80, 100, 120, other gear ratios please contact us.
Parameters
Gear ratio |
30 |
50 |
80 |
100 |
120 |
Rated torque when input 2000r/min (N.m) |
26 |
37 |
60 |
64 |
64 |
Allowable peak torque at start and stop (N.m) |
48 |
93 |
130 |
149 |
159 |
Maximum allowable average load torque (N.m) |
36 |
52 |
83 |
103 |
103 |
Momentary allowable maximum torque (N.m) |
90 |
177 |
242 |
270 |
289 |
Allowable maximum input speed (r/min) |
5500 |
Allowable average input speed (r/min) |
3500 |
Arc seconds |
≤20 |
≤20 |
≤10 |
≤10 |
≤10 |
Dimensions (unit: mm)
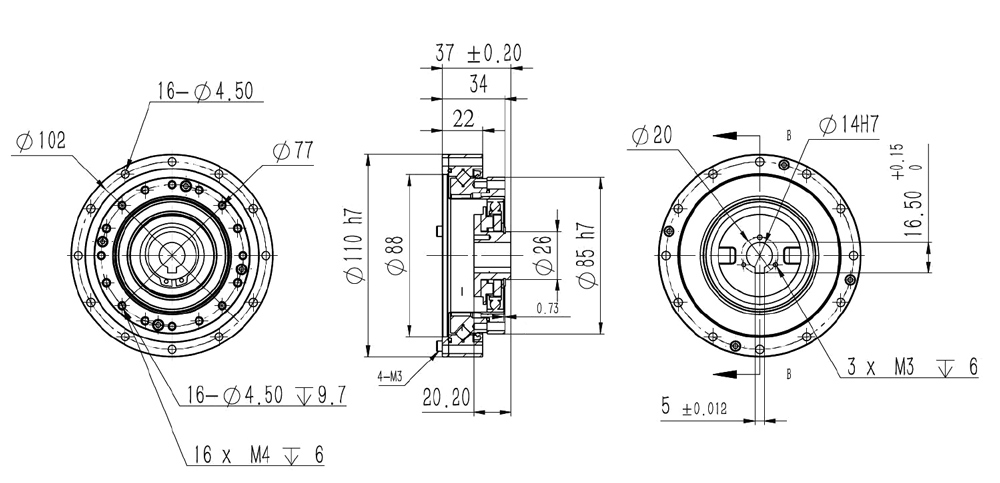
Harmonic Drive Gearbox Applications
ATO harmonic drive gearboxes can be used to optimize the shape of robots, increase precision, increase strength, improve flexibility, etc., and are widely used in industrial robots, numerical control equipment, medical instruments, military and other fields.

Tips: Why is a harmonic drive gearbox so important for robots?
The main function of a harmonic drive gearbox is to reduce the speed and increase the torque while ensuring that the equipment can reliably complete the process tasks and to ensure the positioning accuracy and reset positioning accuracy of the process when the same action is repeatedly performed.
As the three main core components of industrial robot technology, harmonic reducer, AC/DC servo motor and controller directly determine the performance of industrial robots.
The existence of the precision harmonic drive gearbox ensures that the motor runs at a suitable speed, and accurately reduces the speed to the speed required by various parts of the industrial robot, improving the rigidity of the mechanical body and outputting greater torque.