1kW BLDC servo motor for sale, with 1500 rpm low rated speed and 6.3 Nm rated torque and peak torque up to 22 Nm, feedback with 2500 PPR incremental encoder. ATO heavy duty DC servo motors provide features of low rotor inertia, high torque density, high peak torques, low noise, low temperature rising, lower current consumption.
Basic Specifications
- Model: ATO-110AS0410-15
- Rated Power: 1000W
- Rated Voltage: 48V DC
- Rated Current: 28 A
- Rated Torque: 6.3 Nm
- Peak Torque: 22 Nm
- Rated Speed: 1500 rpm
- No-load Speed: 1700 rpm
- Working Efficiency: 85%
- Flange Size: 110mm
- Weight: 8 kg
Technical Parameters
- Incremental Encoder Line: 2500 PPR
- Rotary Inertia: 740 Kg.m2x10-6
- Line Resistance: 0.11 Ω
- Armature Inductance: 50 μH
- Torque Constant: 0.23 Nm/A
- Brake Apparatus Voltage: 24V DC, brake release when powered
- Motor Lead Length: 1 meter
- Back EMF: 15.6 vkr/min
- Protection Grade: IP55
- Insulation Class: Class F
- Certification: CE, ISO
Features
- 1000W DC servo motor with IP55 protection grade and F class insulation structure
- Optimized winding end structure, minimized copper loss and iron loss, small size, light weight, low temperature rise and high efficiency (85%)
- Super coercivity, ATO DC brushless servo motors using NdFe35 permanent magnet material, strong anti-demagnetization ability, stable motor performance
- Low noise, low vibration, low moment of inertia
- High torque, fast dynamic response, wide speed range, strong overload capacity (4 times)
Dimension (Unit=mm)
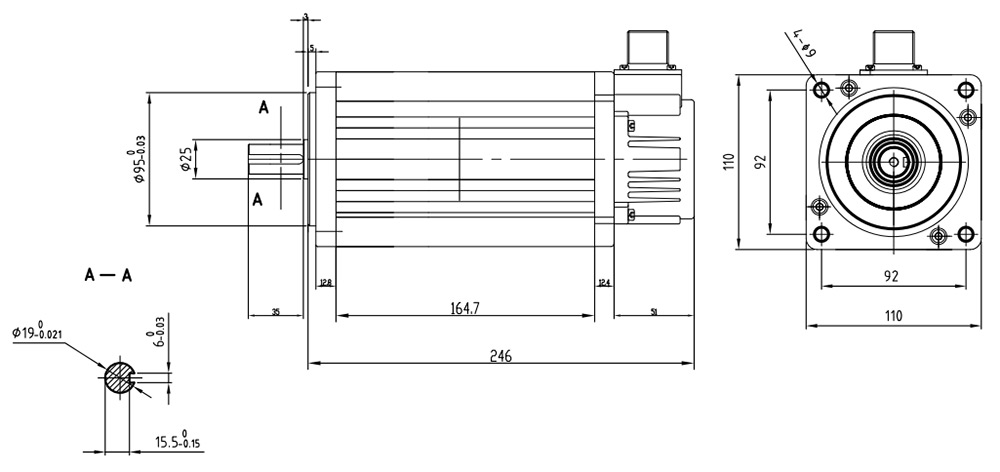
Wiring Definition

Speed-Torque Curve

At no-load point: 6.41(Nm) Speed: 1584.4 (r/min) Current: 27.587 (A) |
At max. efficiency point: 85.3 (%) Torque: 6.41 (Nm) Speed: 1584.4 (r/min) Current: 27.587 (A) Output power: 1063.57 (W) |
At max. torque point: 6.41 (Nm) Speed: 1584.4 (r/min) Current: 27.587 (A) Output power: 1063.57 (W) |
At max. output power point: 1063.57 (W) Torque: 6.41 (Nm) Speed: 1584.4 (r/min) Current: 27.587 (A) |
Details

Tips: How to select inertia of servo motors?
Generally, most servo motors will choose the motor with small inertia, so as to satisfy the high responsiveness of the servo system. Since the greater the rated output moment of the servo motor is, the greater the moment of inertia of its rotor is, so it is meaningless to simply discuss the magnitude of the motor's moment of inertia. In fact, the ratio of the rated output moment to the moment of inertia of the servo motor should be discussed, or the magnitude of the moment of inertia of motors with the same rated output moment.
In general, servo motors will choose servo motors with small inertia to meet the requirement of higher dynamic response. Certainly, servo motors with medium inertia and high inertia can also be chosen according to the specific application environment. For example, when there is no high requirement for fast response, but the requirement for speed control is very precise, and servo motors are often required to run in low speed and low frequency.