Favorable price 1.8 kW brushless AC servo motor, 3-phase 220V AC rated voltage, 6 Nm rated torque, peak torque of 18 Nm, available in a 110mm square flange size. Heavy duty servo motor is widely used in industrial automation, embroidery machines, printing machinery, CNC machine, wood carving and other fields.
Basic Specifications
- Model: ATO110SY-M06030
- Matched Drive Model: ATO-SG-AS302600
- Rated Power: 1800 W
- Rated Voltage: Three phase 220V AC
- Rated Current: 6 A
- Rated Speed: 3000 rpm
- Max Speed: 3600 rpm
- Rated Torque: 6 Nm
- Peak Torque: 18 Nm
- Square Flange Size: 110 mm
- Weight: 10 kg
Technical Parameters
- Number of Poles: 4 pairs
- Rotor Inertia: 1.0x10-3 Kg.m2
- Brake Voltage: 24V DC (Non polar requirement)
- Incremental Encoder Line: 2500/5000 PPR (Optional)
- Absolute Encoder: 17 bit, 23 bit (Optional)
- Insulation Class: Class B
- Insulation and Voltage Resistance: 1500V AC, 1 Min
- Protection Grade: IP65
Features
- Accuracy: ATO AC servo motors realize closed-loop control of position, speed and torque, overcome the problem of stepper motor out-of-step.
- Speed: Good high-speed performance, rated speed can reach 1000-3000 rpm.
- Adaptability: ATO heavy duty servo motors with strong anti-overload capability, able to withstand a load three times the rated torque, especially suitable for occasions with instant load fluctuations and requiring quick start.
- Stable: Our AC brushless servo motors have smooth low-speed operation, no stepping phenomenon similar to stepper motor will occur when running at low speed, suitable for occasions occasions requiring fast response.
- Timeliness: The dynamic response time of motor acceleration and deceleration is short, generally within tens of milliseconds.
- Safety: ATO AC servo motor protection grade is IP65, which meets the waterproof and dustproof requirements.
Installation Dimension (unit: mm)
Servo Motor without Brake Dimension
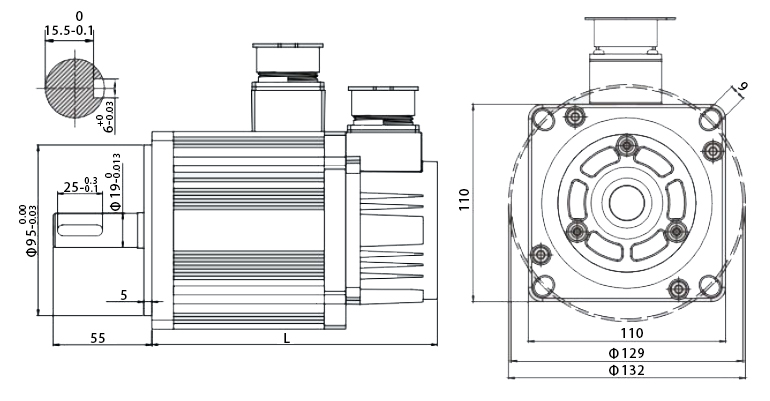
L (Incremental/Absolute encoder): 220 mm
Servo Motor with Brake Dimension
L1 (with brake): 280 mm
Note:
*All above is the standard installation dimension, can be changed according to the customers' requirments.
*Not hit the shaft, or the encoder in the other end would be damaged.
Details

Winding and Encoder Connection
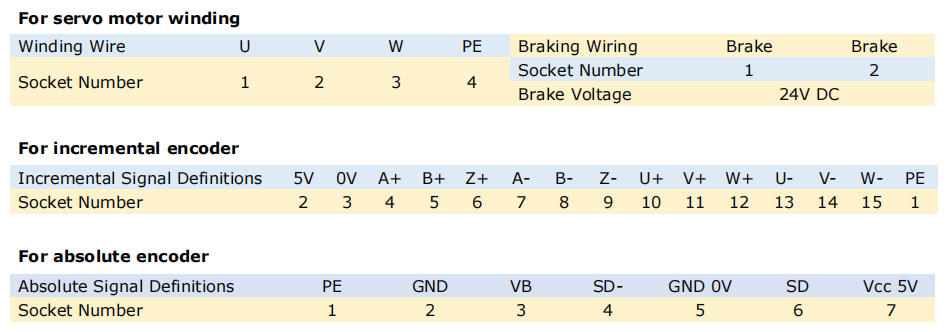
Tips: Speed control a AC servo motor
The rotation speed can be controlled by analog input or pulse frequency. When there is outer loop PID control of the upper computer control device, the speed mode can also be used for positioning. However, the position signal of the servo motor or the position signal of the direct load must be fed back to the upper computer for calculation. Speed mode also supports direct load outer loop detection position signal. At this time, the encoder at the servo motor shaft end only detects the motor speed, and the position signal is provided by the direct detection device at the final load end. This has the advantage of reducing errors in the intermediate transmission process and increasing the positioning accuracy of the entire system.